The spectacular growth of the dimension of the wind turbine has led to the introduction of several interesting technical solutions. Different type of towers (concrete, hybrid, lattice, self-erecting, etc.) and new technical solutions for the foundations appeared in the last decade, trying to have the lowest possible cost of energy.
The rotor of the turbine has followed the same trend. With the impressive size of the blades currently in the market (today we are around 70 meters, the width of a football field) it is not surprising to see a variety of new concepts already in the market or under development.
One of the key issues of very long blades is that it is difficult to optimize them: finding the “sweet spot” for a component exposed to a variety of wind flow characteristics during its operational life is not easy, above all if such characteristics are not uniform along the blade.
The engineers designing the blades are trying to achieve several goals, such as:
- Increase the energy production (maximizing the aerodynamic efficiency and the power extracted from the wind)
- Reduce the loads on the structure
- Create a solution that can easily be transported on public roads and installed with cranes already in the market
- Extend the life of the blades (we are moving to the 25 or even 30 years mark)
All these objectives should be reached with the lowest possible cost.
The term “smart rotor” refer to a variety of technical solutions whose purpose is to increase the production or reduce the loads.
They belong to two categories, passive systems (not controlled by a software or an operator) and active systems.
Among the passive systems the most interesting are:
Vortex generators. Believe it or not, you can buy the elements generating the vortex from 3M (the same company that invented the Post It all around my desk). You can use them to retrofit pitch-regulated turbines sticking them near the root of the blade, where the air flow is separated by the blade (that is, it is “stalled”).
They basically work reducing the separation of the flow, increasing the production 1 or 2 percentage points (they can be a lot of money).
A second passive technology is the bend-twist coupling.
As you will guess from the name it creates a link between the bend and the twist of the blade, with the object to reduce fatigue loads created by sudden inflow changes during turbulent wind conditions.
The wind blowing on the blade is creating 2 forces – “lift” (the one pulling up the blade and making the rotor turn) and “drag” (the one bending the blade backwards). As a general rule the engineers try to minimize the drag and maximize the lift, achieving a high “lift to drag” ratio.
With the bend-twist coupling the loads are reduced because the blades “adapt” its shape changing its shape and the angle of attach when deflected.
This coupling can be achieved changing the geometry of the blade (geometric coupling) or by changing the direction of the fibre inside the composite material (resin + fiber) that constitute the blade.
This interesting technology is currently being investigating by several entities, including a heavy weight such as the Fraunhofer Institute for Wind Energy Systems.
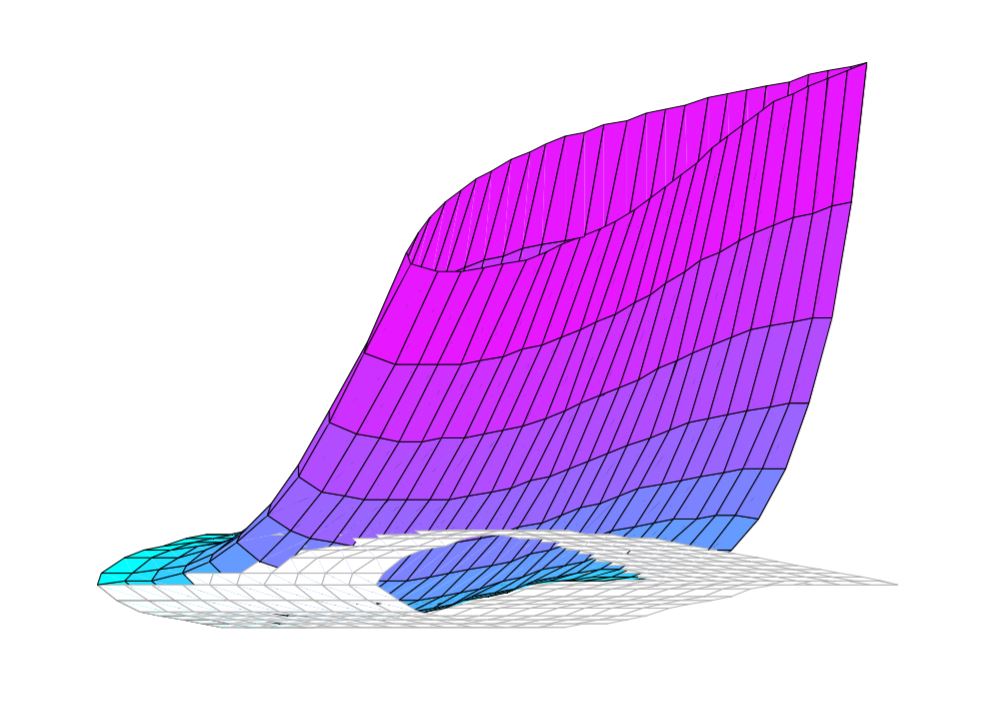
I also described some months ago the serrations. They have a different scope (reduce the noise) but I believe they can be consider a type of passive optimization system.
Leave a Reply