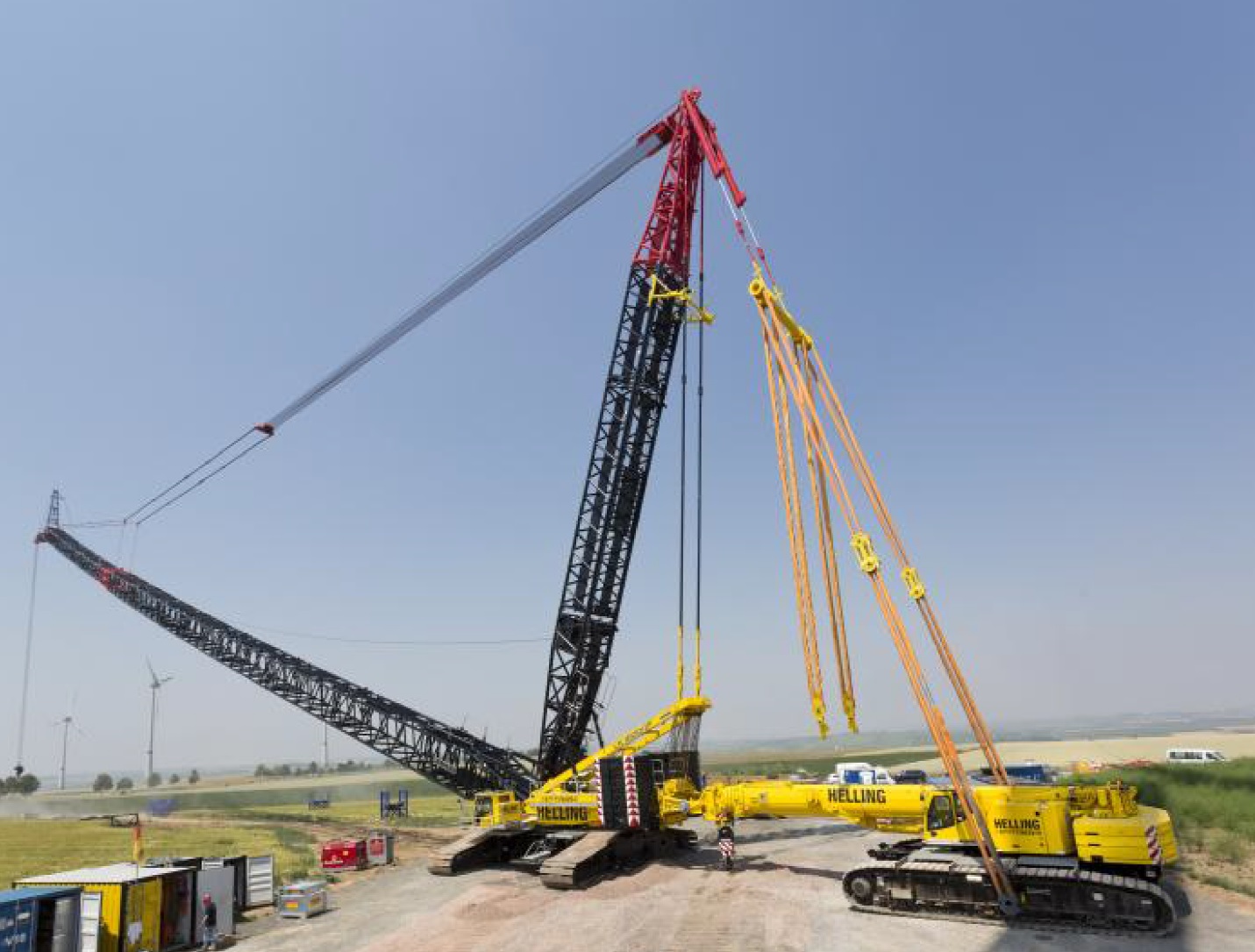
If you are familiar with the huge cranes used in wind farm construction, you will know that a lot of time is consumed rigging and derigging the main crane.
Part of the effort is in the manipulation of the ballast (the counterweight needed to operate safely). The cranes use a modular ballast concept – different steel slabs are added or removed depending on the task to be performed.
These slabs are very heavy – the ones used by Liebherr for instance weight 10.000 Kg each and depending on the crane configuration and the type of lift you can have more than 20 slabs.
Several transport trucks back and forth trips are also needed to move these slabs around the wind farm.
It is important to know that usually the majority of the ballast is needed when the main boom is lowered to the ground (for instance to be dismantled) or it is lifted before the start of the erection works.
I have discovered that a German crane company (Helling GmbH) has developed an alternative technique. It seems that this solution has the blessing and approval of Liebherr, so maybe you want to consider it for your project.
Basically they used one of the hydraulic auxiliary crane as ballast.
In wind farm construction there always at least one “tailing” crane, helping the main crane rotating the wind turbine components in the correct position or assembling and disassembling the main crane itself.
They have had the idea to connect the auxiliary crane to the main crane (in this case, an LR 1600/2 erecting a Senvion turbine with hybrid tower).
The solution worked perfectly, and the 150 meter boom was lowered and lifted without problems.
Leave a Reply