How are the blades of the wind turbines installed?
Although in general each wind turbine model has only one installation procedure, several technical alternatives have been developed through the years.
The quicker and easier method is probably to assembly the rotor on the ground. The three blades are connected to the hub and then lifted together in what is called “rotor installation” or more colloquially “the cross” (I guess because during the lift it vaguely remember a crucifix).
The main problem is that this solution need a lot of space. Additionally, as the blades are becoming bigger and bigger, it would be impossible to lift the weight of three blades at a height of more than 100 meters with the cranes currently available.
Another solution, very uncommon (actually I have never seen it in the real world) is the “bunny ears” method. Nacelle and two blades are lifted together, resembling (if you have a vivid imagination) the face of a bunny with two long ears.
The solution used more frequently nowadays is the single blade installation. The blades are lifted one by one and connected to the hub, usually horizontally although some turbine models are designed for an inclined or even vertical blade position.
Liftra, a company active in the wind industry, developed a tool called “blade dragon” that allow blade installation in every position.
The concept can be interesting in several situations – for instance if you want to disassembly a blade for repairing, you could use a smaller crane disassembly a blade in vertical position (that is, with the tip pointing downwards).

The single blade installation need a specific “blade lifting tool”. Such tools usually provided by the turbine manufacturer and are designed to fit a specific blade model.
Often there aren’t so many tools available (they are expensive, so their number is kept to a minimum) they can be a source of problems (for instance if the tool breaks or arrives late).
You will also need a second tool to turn the rotor, called “rotor turning tool” or “turning gear”.
As the blades have to be installed horizontally, you will need to rotate the hub after the first blade is installed to have an empty socket in the right position, and repeat the procedure after the second blade is installed.
Those turning tools are hydro-mechanical. A power source is connected to a pump generating the pressure needed to rotate the gears.
The standard solution is to connect the tool to the disk brake used to stop the turbine in case of emergency. The brake disc wheel is toothed, allowing efficient coupling with the tool.
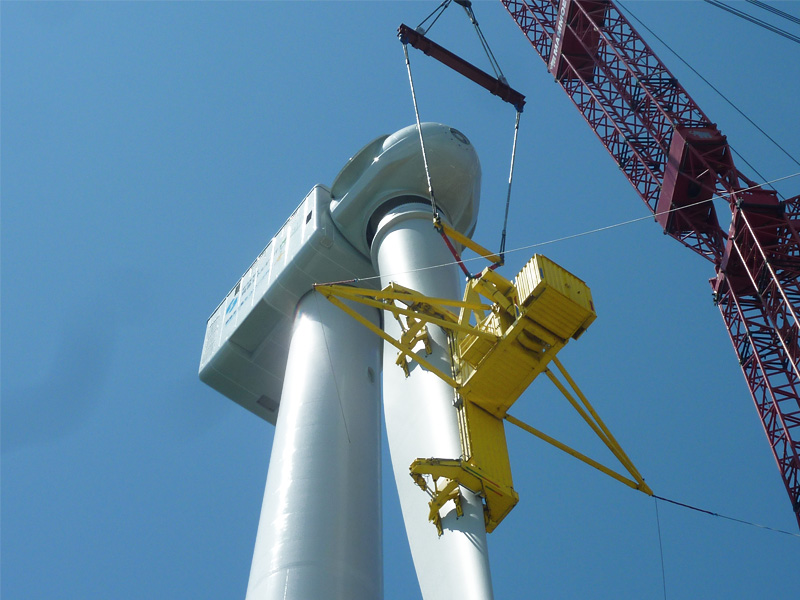
The single blade lift is generally more time consuming, as you will need 4 different lifts (one for the hub and three for the blades) compared to the rotor lift.
Leave a Reply